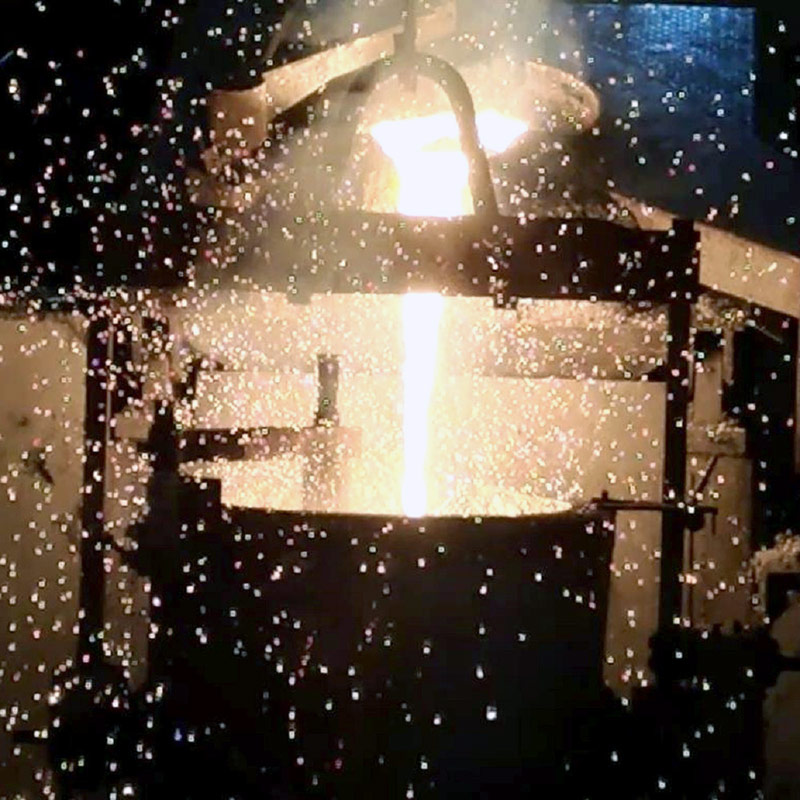
Production Capability
Our Core Technology
As a professional casting foundry for more than 25 years, Teamco is capable of providing worldwide industrial customers good quality machined metal parts in diversified applications. To focus on the production of Valve Metal Parts, we built up own lines of forging and precision machining as well. This makes Teamco a professional supplier specializes in valve parts specifications compliant to international standards such as API or NACE. To serve more customers in diversified segments, Teamco expands to more production capabilities and value-added services to solve customer’s problems, such as stamping, electric polishing, nitriding and zinc phosphating, etc.
We are competitive in providing customers solutions in segments of oil & gas pipeline maintenance, mechanical equipment, instruments and measurements, hydraulics control, sensing equipment, building locking components and marine hardware. We are professional in OEM and capable of ODM in reverse engineering design to parts subassembly. In high volume or high product mix, we provide stable product quality and services to win customer’s trust and buildup long-term partnership.
MAIN PRODUCTIONS & SERVICES:
•Investment Casting: Tooling Die Design and Fabrication, Wax Mold, Shell Mold, Pouring, Heat Treatment, Sand Blasting and Casting
•Forging (Closed-Die): Tooling Die Design and Fabrication, Raw Material Cutting & Heating, Shaping (Rough Shape, Cavities/ Dimensions and Final Dimensions), Heat Treatment and Shot Blasting
•Precision Machining: High Precision Turning, Milling, Drilling, Tapping, Broaching, Grinding; Compound CNC Swiss Type Automatic Lathe/ Milling; Compound CNC Turret Type Automatic Lathe/ Milling
•Surface Treatment: Surface Grinding, Electropolishing, Plating (zinc, nickel, hard-chrome), ENP (Electroless Nickel Plating), Coating (zinc phosphating, thermal spraying, Tungsten Carbide, HVOF and MoS2) and QPQ (Quench-Polish-Quench)
•Heat treatment: Nitriding, Normalization, Quenching, Tempering
•Metal Stamping: Tooling Die Design, Stamping (punching, blanking and piercing), Forming (drawing and bending), Trimming and Sand Blasting
•Non-Destructive Tests: UT (Ultrasonic Testing), MT (Magnetic Particle Inspection) and PT (Penetrant Inspection)